by Sarah Turnbaugh
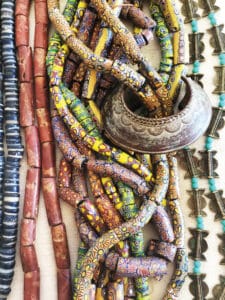
Millefiori beads made in Venice, Italy, reached lofty technical and aesthetic heights in the late 1800s to early 1900s. The colorful, stunning-looking beads seem almost magical – then we learn that they were handmade using laborious, time-consuming methods in small factories and lone artisans’ homes. Glassworkers aptly called these seductive creations “millefiori,” meaning “a thousand flowers.” The beautiful Italian name, like the remarkable beads themselves, caught on.
ORIGINS
Glass beadmaking began in ancient times, long before the first Venetian millefiori beads appeared. First, the ability to create glass itself had to be developed. Glazed objects were being made in Egypt and Mesopotamia (modern-day Iraq) over 5,000 years ago. Powdered silicate glazes were applied on the surfaces of objects like Egyptian faience mummy beads, which—when heated with fire—vitrified the powder in a self-glazing process. Egyptian faience beads have earthenware bead cores coated with opaque blue-green glassy glazes.
Evidence of glassworks found at Tel El Amarna in Upper Egypt dates from the Eighteenth Dynasty, more than 3,500 years ago. At around the same time, in about 1600 BCE, a glass goblet excavated at Tell al-Rimah in Mesopotamia was made using thin, malleable, colored glass rods that were applied up and down on the surface of a sand or mud core to create the goblet’s zigzag pattern. By 3,000 years ago, glass vessels and glass beads likely were already being made and used in many locations beyond Egypt and Mesopotamia, including Rome, from where the knowledge spread widely throughout the Empire.
Mosaic glass beadmaking in Venice itself dates to the days of the Venetian merchant Marco Polo, who brought back beautiful beads from Asia when he returned from his travels in 1294 CE. Over two thousand years after mosaic glassmaking first had been developed in western Asia, eager Venetian glassworkers reinvented the ancient method. In her book The History of Beads, Lois Sherr Dubin more fully discusses the development of Venetian beadmaking in the broader context of its times.
Ultimately, Venice established an official Glassmakers Guild to regulate and control glass production in the city and to make sure that trade secrets were not leaked out to other parts of Europe and Asia. Venice so jealously guarded the highly specialized skill and knowledge involved in the multi-stepped mosaic glass beadmaking process that it moved every glassworking furnace to Murano early on. Officially, Murano’s isolated location on a harbor island protected the city of Venice in case of accidental glassworks fires. But, by sequestering all the operating glassworks in this way, secrecy also could be preserved for the complex skill.
Native peoples on other continents coveted the colorful Venetian mosaic glass beads, nowhere more than in Africa. From the 1400s on, these valued and costly beads became a major commodity traded to Africa, and far less so to North America and Asia. Beadmaking and widespread demand for these beads enabled the small republic of Venice, with Murano as its center of production, to dominate international trade bead markets for generations.
WEST AFRICAN MARKET
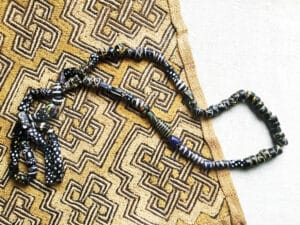
During the African colonial period extending into the eighteenth century, shiploads upon shiploads of glass trade beads from shops in Venice were reaching ports on West African shores, where many Native peoples enjoyed wearing these colorful millefiori beads. Angela Fisher, in Africa Adorned, illustrates various ways in which Africans mixed Venetian beads into ethnic articles of dress, often wearing trade beads alongside other locally-made accouterments like glass, ivory, and metal accessories.
Around 400 varieties of beads were being made in Venice by the mid-19th century, but individual African tribal groups favored no more than five to ten colors, sizes, or shapes. Mosaic glass beads not only were bright, decorative elements of personal adornment but they also functioned as an important form of Native currency. During the African colonial period, Triangle Trade ships brought Venetian beads and other trade goods to West African Gold Coast ports, where huge numbers of beads of certain shapes and colors were traded and exchanged widely for valued commodities like palm oil, ivory, and gold. From West Africa, the ships traveled onward to the West Indies plantations, where African resources were exchanged for produce. Then, the produce-laden ships finally returned to Europe, before once again setting out.
In Native Africa, Venetian glass beads remained in high demand throughout this long period. Even into the 1950s, the Zulu, alone, were importing over 40 tons of beads a year. Glass beadmaking designs had became more complex through the previous three or four centuries as Venetian workers developed new methods.
For about a century or longer, Venice appears to have lost the knowledge of millefiori mosaic glass beadmaking. Venetian glass beads that date to the early to mid-1800s are simpler. But, by the mid- to late 1800s, its artisans rediscovered the complicated, multi-step technique and took it to new heights. The millefiori beads were made primarily in Venice in the late 1800s, and most were exported to Africa for trading.
In the first half of the 20th century, the German distributor J.F. Sick & Co., with offices in Venice and Holland, was the major supplier of millefiori beads to West Africa. When the firm closed its office in Venice in 1964, it donated its sample collection of about 22,000 Venetian glass beads and sample cards to the Tropenmuseum in Amsterdam. This extensive collection, available for viewing online, courtesy of the Tropenmuseum, provides an invaluable resource for current researchers and collectors.
ENDURING POPULARITY
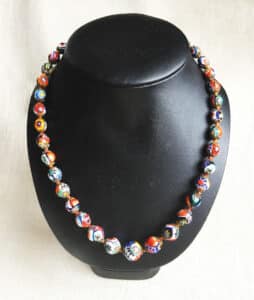
In the mid-twentieth century, a new style of Venetian millefiori mosaic glass bead was made and strung into Italian necklaces for sale to tourists. At the same time, tourists, Peace Corps workers, and collectors also were acquiring large numbers of the antique millefiori trade beads in Africa during the third quarter of the 20th century. Most of the beads illustrated in this discussion represent just a few strands of many thousands that were collected in Mali and other countries in the early 1960s. During this decade, antique millefiori beads were incorporated into popular fashion jewelry here in the United States.
The antique Venetian millefiori beads also may have inspired hippies, or flower children, in Los Angeles and other communities to make candy glass beads, or “love beads,” featuring a single flowery millefiori-like slice or two. These beads were often combined with the anti-war peace symbol in casual necklaces and jewelry.
In Western life today, the luscious-looking antique millefiori beads of more than a century ago still inspire designers of distinctive contemporary and fashion jewelry pieces. A single unique millefiori bead, or a strand of many beads sporting a combination of colors and designs, may be used to create a stunningly patterned necklace, ring, earrings, or other desired accessories. Each is guaranteed to be one-of-a-kind.

When they can be found, antique millefiori beads may be costly, ranging generally between $15 to $35 per bead, or as much as several hundred dollars per strand. The most expensive generally are curved “elbow” beads that are over 1½” long with no flaws or surface chips. Nevertheless, despite their rarity and costliness, the beads continue to be sought after to this day. Some so-called millefiori beads are being produced in several countries today including China, as well as in Venice itself. However, few contemporary beads achieve the superior quality and aesthetic appeal of the late 19th to early 20th century masterpieces.
PRODUCTION
The sheer number of millefiori mosaic glass beads that found their way to market in the worldwide trade network is all the more remarkable when we realize that they are handmade, using multi-stepped, time-consuming methods. Each bead differs slightly from every other. Both Jamey Allen (www.beadcollector.net) and the Picard Trade Bead Museum (www.picardbeads.com) have discussed the complex process of making millefiori beadmaking techniques in detail. A brief consideration of basic methods follows.
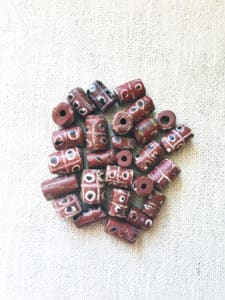
During each stage, described below, an artisan’s creativity and ability come into play. Even beads built using the same initial color sequence for the composite cane can end up looking quite different from one another, depending upon the beadmaker’s choices and intended design. As an illustration, the Text Box and Image below illustrates how beads exhibiting the same color sequence of yellow-white-red-blue varies according to a beadmaker’s preferences and choices, resulting in significant visual differences in these finished beads, called “eyes,” “flowers,” and stars.
To fabricate millefiori beads, artisans first prepare their materials, which consist of colorful glass rods called canes. To do so, beadmakers start with a glob or gather of molten glass. A pair of artisans attach two metal pontils on opposite ends of it. They back away from each other for a distance, thus drawing out the gather to form a long, thin glass cane that quickly cools and hardens. The glassworkers repeat this process many times to produce multiple glass canes of different colors.
Next, a selection of these different colored glass canes is bundled to form a pleasing arrangement and heated, fusing them together into a multicolored composite cane with a flower-like or patterned cross-section. This composite cane is, in turn, heated, drawn out, cooled, and cut into thin slices that each reveal the colorful flower-like cross-section.
Finally, the delicate slices are pressed or embedded onto the surface of a malleable, wire-wound glass core and fused to form the finished bead. After cooling, the wire is removed, and individual beads are cut into various lengths that are tumbled to smooth the sharp edges. The artisans’ work is done. Their millefiori beads are ready to go out into the world for all to enjoy.
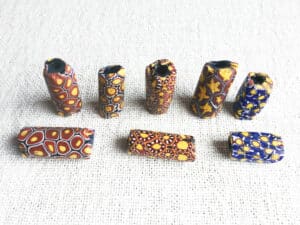
Each upright bead in this image is built using the same color sequence from the center out—yellow-red-white-blue—to create the five distinct bead patterns. Artisans made different choices at each step, thus producing these five distinct designs.
Left to right:
1) “Eye” bead – concentric layers of canes form the “eye” pattern;
2) Flower-like bead with concentric layers, and bumpy white and blue layers consisting of tiny canes gathered around the central colors;
3) Flower-like bead, with its third layer formed by alternating white and blue colored tiny canes. More complex, as the preformed, composite cane was then dipped in two additional layers – red and yellow;
4) Star bead with a central yellow cane that was inserted into a star-shaped mold once, then layered with red, white, and blue colors, and given an overall hexagonal shape by pressing the still malleable surface before slicing and pressing onto the core; and
5) bead built similarly, with finished design units fused together, and the surface of the finished bead molded or flattened on four sides.
Related posts: