by Kary Pardy
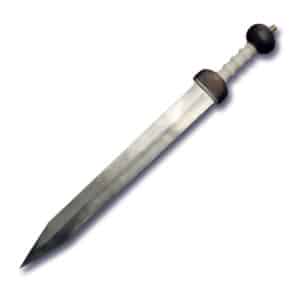
sharply-pointed, double-edged sword and its design had evolved over the centuries to be the ideal weapon for the legions of the Roman Empire. It was forged from high-grade steel and was primarily suited for the Roman fighting style, where shield usage was heavy and swords were called upon to thrust and stab through the shield wall. In their book From Sumer to Rome: the Military Capabilities of Ancient Armies, historians Richard Gabriel and Karen Metz wrote that in the hands of a highly trained legionnaire, the gladius “was the most deadly of all weapons produced by ancient armies, and it killed more soldiers than any other weapon in history until the invention of the gun.” photo: Wikipedia
There are lots of reasons to be drawn to edged weapons, and their beauty and history are chief amongst them. Each piece carries with it a complicated past that is directly connected to our most violent and sometimes, most noble, heroic stories. Whether you’ve got a parade sword or your ancestor’s Bowie knife, these are blades that shaped history, and this article will take a closer look at the technology shaping those antique blades.
When discussing what makes a sword or a knife “good,” specialists are evaluating four key criteria: strength, flexibility, hardness, and balance. Over the years access to metals has changed, but these goals have remained as necessary determinants of a blade’s quality. A blade must be hard enough to support its length, flexible and strong enough to take a beating in combat without breaking, and balanced enough to be used without over-compensation. Shirking on any one of these traits could be a matter of life or death, and while bladesmiths might be called upon to shift styles in the face of military changes, these principals always remained of the utmost importance.
What made the world’s famous blades so cutting edge?
To appreciate weapons development, it’s important to understand that new technologies arose out of demand and available resources. Early weapons of copper and bronze were typically cast, not forged, but bronze smiths used varying amounts of tin in the different parts of the blade depending on what was needed. Early Chinese swordsmiths used a strong, fracture-resistant low-tin alloy in the center of their swords, and cast the edges in high-tin bronze, which was harder and could hold a sharper edge. With the influx of steel technology, edged weapons changed. The Roman Gladius and the Viking Ulfberht are legendary steel weapons that stand out as technological milestones in bladesmithing, but none can hold a candle to Japanese swordsmiths for their painstaking devotion to hardness, flexibility, strength, and balance.
Samurai Katana
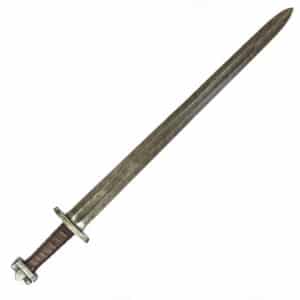
West until the Industrial Revolution, making the
origin of these fine pieces a topic of debate amongst historians. photo: Battling Blades.
The Samurai katana is perhaps the most famous sword style of all time. On a very broad scope, Japanese brilliance with edged weapons really started to shine through during the Heian Period (794-1191). While previous swords had been straight and were perfect for the fighting style of the time (lots of thrusting and stabbing), this era saw the more frequent use of horses in combat. Warriors needed a better weapon, and the new, curved swords (called tachi) met the demand for a weapon that could slash and be held in one hand. To achieve this new blade, swordsmiths increased the length but added ashi, strips of soft steel, along the hardened edge to protect the blade when clashing in combat. Blade technology leaped forward again during the Kamakura Period (1185-1333). After a series of devastating attacks by the Mongols, Kamarura warriors saw the necessity of better weapons technology. Some advancements included adding a low-carbon steel core into the blade and lengthening of the hardened edge, making the blade broader with a larger point. The katana were developed during this period and honed in the next, taking over for the tachi and becoming more than a weapon – they were art.
To craft a katana, one must select the right materials, and combine iron and carbon by heating sand for 72 hours in a traditional tartara furnace to achieve a temperature of 2,200-2,700 degrees Fahrenheit. The resulting nuggets are called tamahagane, and a swordsmith must form them into a workable block and hammer it thin before scoring it with an axe, folding the piece over on itself, and placing it back in the furnace. The folding process, which is called shita-kitae, can be done lengthwise or diagonally (occasionally swordsmiths do both to achieve the desired pattern) and happens anywhere from eight to sixteen times. The folding takes the varied carbon content in the original tamahagane block and mixes it, just as one would combine ingredients in a bowl, removing impurities as you might remove the lumps in your mixture.
The swordsmith will then use a hammer to draw out the piece of metal, and depending on the carbon content of the metal, will decide what part of the final sword the piece will become. Different swordsmiths craft their blades with different pieces, each selected for the ideal properties needed for each area of the blade. The edge requires a very hard steel, while the sides and back may be made of a more malleable, spring steel to give added flexibility and strength. Steel properties are also honed during the tsuchioki process. When the smith was satisfied with the shape of the sword, he would coat it in several layers of a wet clay mixture, the exact formula of which is a secret recipe for each swordsmith. The clay-coated sword would then be heated once more before being quickly quenched with water. The heating and rapid cooling within the clay created the katana’s graceful curvature and extra strength and hardness to the edge of the blade. Finally, the blade would be sent out for polishing, which could take weeks using a series of increasingly-fine polishing stones to create that famous mirror shine.
Around the World
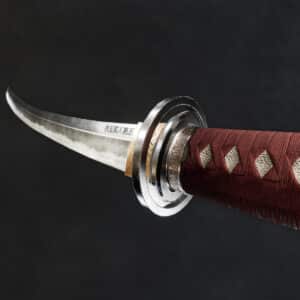
Goro Nyudo Masamune, who was proclaimed the chief swordsmith of Emporer Fushimi when he was only 23. Masamune developed and perfected the technique of folding and blending hard and soft steel together to make something stronger and more deadly than any sword being made around the world. His most famous creation, the Honjo Masamune (named for the general who was its first owner), was fabled to be so well crafted, its many layers tapered to a point that was just one atom thick. Sadly, the sword was lost to public record after World War II and has never been recovered. This photo depicts a fan’s reproduction of the blade since images of the legendary blade are lost as well. photo: Reddit user U/Chuwak.
While the Japanese katana is an extreme example of swordsmithing at it’s finest, similar principles applied for edged weapons around the world. A smith would start with a central bar that was either folded upon itself and drawn out or welded to other pieces, placing the softest metal towards the interior. Then the future blade was shaped and tapered to create an edge and a point. Fullering, a technique that created a ridge (or ridges) running down the length of the blade, gave the whole piece greater structural strength. Once shaped, a smith would use temperature to finish off their work. Some techniques called for evenly heating and slowly cooling the finished product to remove any stresses on the blade, others involved heating and cooling at different rates on different parts of the blade to create specialized effects, such as a cutting edge that was harder than the overall body of the weapon.
Stock Removal Technique
While there are still artisans that hand-forge their blades, most of today’s knives and swords, and indeed, most blades made from the 19th and 20th centuries onward, are made with the stock removal technique. This efficient and often mechanized process involves taking a piece of metal that is larger than the final product and cutting, grinding, and polishing it down to the desired shape and finish. While the initial core may be strong because of advances in steel technology, there is something special about hand-forged weapons and calling upon the compiled wisdom of weapons experts before you to shape something that specifically addresses the challenges a blade and its warrior may face. You can collect edged weapons for their direct or representative history, or for their decoration, but you can also collect them for their painstaking craftsmanship, which in itself is a victory.
Related posts: